Litter is a huge problem—around the globe and even floating above it. Debris left over from rocket launches and defunct satellites are whizzing around in space with increasing density. There are approximately 9,000 man-made objects orbiting the Earth, equating to more than 5 million kilograms of satellites that will become space debris once they are no longer useful or stop working. Just like litter on Earth, space debris also has to be disposed of, but collecting it is much harder than just picking up trash.
A new study, published in Transactions of the Canadian Society for Mechanical Engineering, presents the design of a satellite with a mechanism intended to capture tumbling space debris. The satellite features an arm that can be deployed with a unique multi-fingered cage that can capture debris whirling through space.
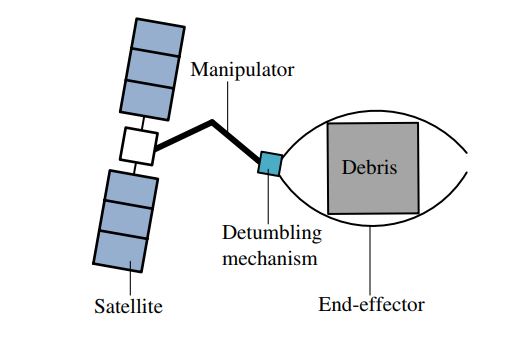
A satellite fitted with an arm and multi-fingered cage is designed to capture tumbling space debris.
There are several challenges that the team from Harbin Institute of Technology in China faced when contemplating their design. The first is that space debris is moving, or tumbling, on three different axes. Techniques to stop this motion include contact methods, which require rather precise maneuvers when capturing the floating object, and contactless methods, which require complex equipment and lots of energy to stop the object from tumbling.
The proposed design is a contact method that consists of a cage with multiple finger-like tubes that surround the object. Once the object is captured in the cage, it uses friction to slow down the object’s movements. This caged design removes the requirement of precise movements that other contact detumbling methods need because it surrounds the free-floating object on all sides so that the object doesn’t get pushed away. It also is a simple design that has an added benefit of being compactable, making it ideal for space travel.
The fingers of the cage are made from carbon-fibre, a strong, lightweight material, and each finger can be compressed down using hinges along each tube. This addressed another one of the team’s challenges: a compactible size during the launch of the satellite to space. A rope system is aligned along the palm of the cage (or hand) to ensure that the fingers do not deploy during space flight. Once in orbit the palm is rotated which releases the rope and the hinges release the tubes of carbon fibre that make up the fingers.
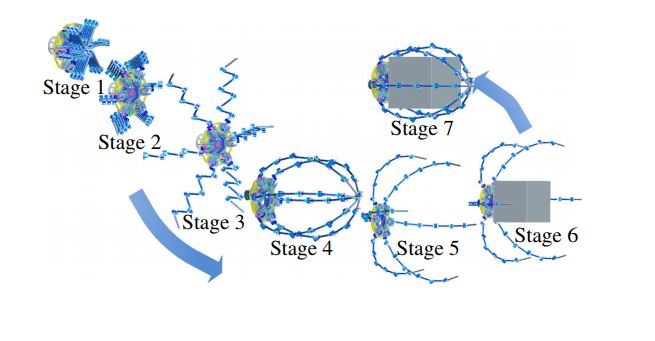
Schematic diagram of multi-fingered cage deployed to slow down and capture space debris.
Finally, once the cage captures an object, it still must stop the object’s tumbling movements. This is done by applying torque to the object and slowing it down using friction. Feedback of forces and torque are sent to the manipulator. Then torque is applied through two friction disks to stop the rotation of the object along the three axes.Because of the high costs of testing the mechanism on the ground, only computer simulations have been run to test the mechanism.
Read the full study: Design of a novel deployable mechanism for capturing tumbling debris in Transactions of the Canadian Society of Mechanical Engineering.